What is Porosity in Welding: Common Resources and Effective Solutions
What is Porosity in Welding: Common Resources and Effective Solutions
Blog Article
The Science Behind Porosity: A Comprehensive Overview for Welders and Fabricators
Comprehending the intricate systems behind porosity in welding is essential for welders and producers aiming for impeccable craftsmanship. From the composition of the base products to the ins and outs of the welding procedure itself, a wide variety of variables conspire to either aggravate or reduce the existence of porosity.
Recognizing Porosity in Welding
FIRST SENTENCE:
Examination of porosity in welding reveals essential understandings right into the stability and high quality of the weld joint. Porosity, characterized by the existence of cavities or gaps within the weld metal, is a common problem in welding processes. These spaces, otherwise appropriately addressed, can endanger the architectural stability and mechanical homes of the weld, resulting in prospective failings in the completed item.

To detect and evaluate porosity, non-destructive testing approaches such as ultrasonic testing or X-ray assessment are typically used. These techniques enable for the recognition of inner issues without jeopardizing the honesty of the weld. By assessing the size, shape, and distribution of porosity within a weld, welders can make enlightened choices to boost their welding processes and accomplish sounder weld joints.
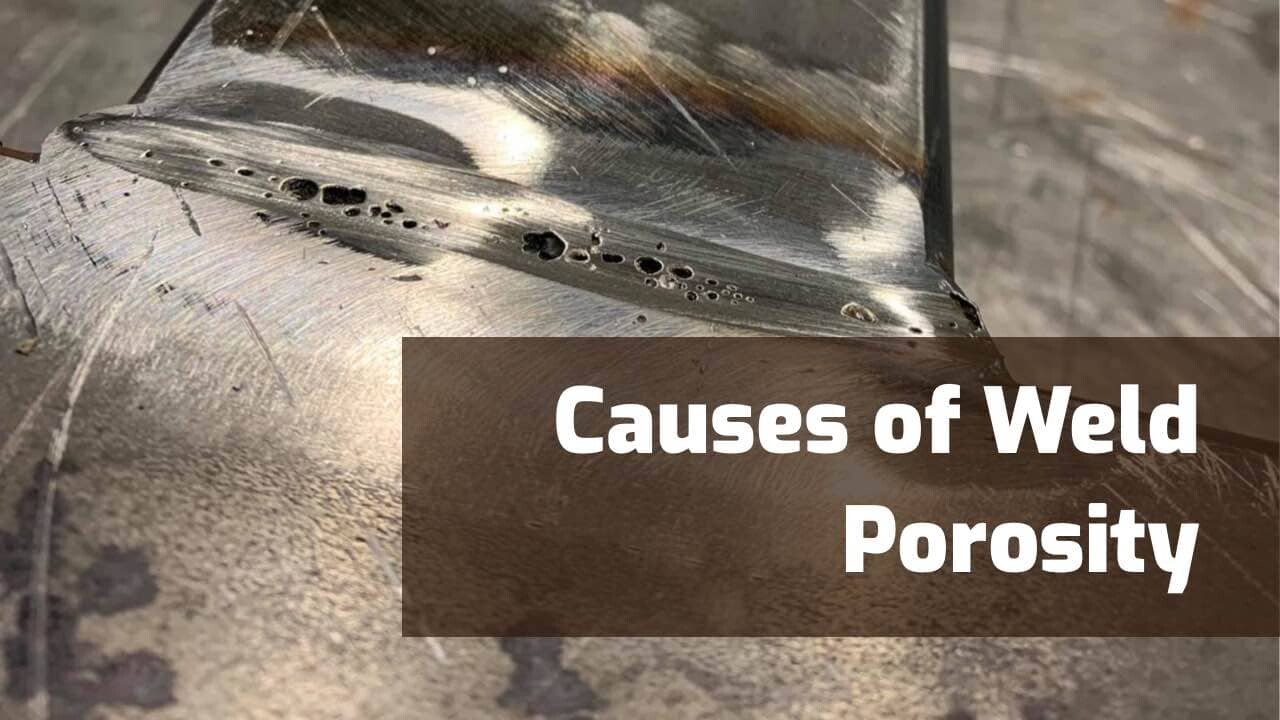
Variables Influencing Porosity Formation
The occurrence of porosity in welding is affected by a myriad of aspects, ranging from gas securing efficiency to the details of welding criterion setups. Welding criteria, including voltage, present, travel rate, and electrode kind, also impact porosity development. The welding strategy utilized, such as gas steel arc welding (GMAW) or protected metal arc welding (SMAW), can affect porosity development due to variants in warmth distribution and gas insurance coverage - What is Porosity.
Results of Porosity on Weld High Quality
The presence of porosity likewise weakens the weld's resistance to rust, as the caught air or gases within the gaps can react with the surrounding environment, leading to destruction over time. In addition, porosity can impede the weld's capacity to withstand pressure or impact, more threatening the total top quality and reliability of the welded framework. In important applications such as aerospace, vehicle, or structural buildings, where security and sturdiness are extremely important, the damaging effects of porosity on weld high quality can have severe effects, emphasizing the value of decreasing porosity via appropriate welding methods and treatments.
Strategies to Decrease Porosity
To enhance the top quality of welded joints and make sure architectural stability, welders and producers utilize details techniques targeted at minimizing the formation of gaps and tooth cavities within the material throughout the welding process. One effective approach to reduce porosity is to ensure correct material prep work. This consists of detailed cleaning of the base steel to eliminate any pollutants such as oil, grease, or dampness that can add to porosity formation. In addition, making use of the appropriate welding specifications, such as the appropriate voltage, present, and take a trip speed, is critical in stopping porosity. Preserving a regular arc length and angle during welding additionally aids lower the likelihood of porosity.

Utilizing the proper welding technique, such as back-stepping or using a weaving activity, can additionally aid disperse warm uniformly and decrease the possibilities of porosity development. By carrying out these techniques, welders can successfully minimize porosity and produce premium bonded joints.
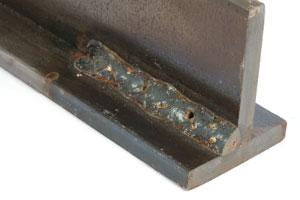
Advanced Solutions for Porosity Control
Implementing innovative modern technologies and cutting-edge methods plays a crucial function in achieving remarkable control over porosity in welding procedures. One sophisticated option is the use of advanced gas mixes. Securing gases like helium or a combination of argon and hydrogen can help in reducing porosity by offering better arc stability and enhanced gas protection. Furthermore, employing innovative welding techniques such as pulsed MIG welding or modified environment welding can additionally assist alleviate porosity concerns.
One more advanced remedy includes making use of sophisticated welding equipment. For circumstances, utilizing tools with integrated attributes like waveform control and advanced source of power can improve this link weld high quality and minimize porosity dangers. Furthermore, the application of automated welding systems with precise control over specifications can substantially reduce porosity problems.
In addition, incorporating innovative surveillance and assessment technologies such as real-time X-ray imaging or automated ultrasonic testing can help in spotting porosity early in the welding procedure, permitting immediate corrective actions. On the whole, integrating these sophisticated options can considerably boost porosity control and boost the overall high quality of bonded components.
Conclusion
In verdict, comprehending the science behind porosity in welding is crucial for welders and fabricators to create high-quality welds. By recognizing the elements influencing porosity formation and carrying out methods to decrease it, welders can enhance the overall weld quality. Advanced remedies for porosity control can further like this improve the welding procedure and ensure a strong and reputable weld. It is my link very important for welders to continually enlighten themselves on porosity and implement ideal techniques to attain ideal outcomes.
Report this page